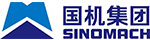
文章出處:知識(shí)中心 網(wǎng)責(zé)任編輯: 洛陽軸承 閱讀量: 發(fā)表時(shí)間:2021-07-14 08:35:59
解決措施
1 密封圈
1.1 選擇質(zhì)量可靠的密封圈材料
國內(nèi)密封圈的抗老化、抗磨損等關(guān)鍵性能與國外還有一定差距,當(dāng)前大多風(fēng)電機(jī)組制造商采用成本較高的進(jìn)口密封圈材料。
1.2 改善密封圈的結(jié)構(gòu)
目前國內(nèi)大部分變槳軸承密封圈采用類似雙唇的結(jié)構(gòu),如圖4所示,結(jié)構(gòu)簡單,防止內(nèi)部漏脂的能力有限,因此在原有結(jié)構(gòu)基礎(chǔ)上進(jìn)行優(yōu)化,將雙唇結(jié)構(gòu)改為多唇結(jié)構(gòu)(圖5) ,同時(shí)增加2道直密封唇加強(qiáng)防泄漏效果,其安裝示意圖如圖6所示。
圖4 變槳軸承原密封結(jié)構(gòu)
1—凸臺(tái);2—主密封體;3—防塵唇;4—第3道封油唇;5一第2道封油唇;6—第1道封油唇;7—第1道直密封唇;8—第4道封油唇;9—第2道直密封唇
圖5 新型防泄漏密封圈截面示意圖
圖6 新型防泄漏密封安裝示意圖
第1道封油唇前端與變槳軸承內(nèi)圈的外圓表面緊密接觸,末端與外圈的內(nèi)圓表面緊密接觸,其外側(cè)凸起的弧面有利于抵消變槳軸承內(nèi)部的潤滑脂壓力,可防止?jié)櫥瑥牡?道封油唇與內(nèi)外圈之間的間隙泄漏。
第2道、第3道封油唇外形呈魚尾狀,其與內(nèi)圈外圓表面上的密封槽接觸,兩者之間存在微小的間隙,丁晴橡膠密封圈具有一定的彈性,既能保證變槳軸承正?;剞D(zhuǎn),又能防止從第1道封油唇泄漏的潤滑脂繼續(xù)向外泄漏。
第4道封油唇與外圈的嵌槽接觸,可防止變槳軸承泄漏的潤滑脂繼續(xù)向外泄漏。
防塵唇外形呈魚鰭狀,末端與內(nèi)圈的外圓表面緊密抵靠,其外側(cè)面凸起的弧面不僅保證了防塵唇與內(nèi)圈緊密抵靠,而且利于加工。防塵唇具有雙向防護(hù)的特點(diǎn),既能防止泄漏的潤滑脂繼續(xù)向外部泄漏,又能防止空氣中的灰塵、雜質(zhì)或其他有害物質(zhì)進(jìn)入到變槳軸承內(nèi)部導(dǎo)致溝道磨損或發(fā)熱卡死,造成風(fēng)電機(jī)組無法正常工作,甚至出現(xiàn)重大事故。
第1道、第2道直密封唇與外圈表面接觸,可防止泄漏的潤滑脂繼續(xù)向外泄漏。
凸臺(tái)位于主密封體上,上表面為平面,同時(shí)與防塵唇之間預(yù)留了安裝工具操作空間,可使用帶滾輪結(jié)構(gòu)的操作工具沿凸臺(tái)上表面前后滾壓,將密封圈壓實(shí),從而保證密封圈的密封效果。
新型防泄漏密封圈整體外形呈魚骨形,采用1道防塵唇、4道封油唇、2道直密封唇,可有效杜絕軸承內(nèi)部潤滑脂向外泄漏。
1.3 合理維護(hù)并及時(shí)更換損壞或老化的密封圈
必須嚴(yán)格按規(guī)定的工藝安裝或維護(hù)密封圈,避免密封圈安裝不合格或密封圈損壞的情況。對(duì)漏脂變槳軸承密封圈進(jìn)行檢查,如發(fā)現(xiàn)密封圈存在老化、磨損嚴(yán)重、破損、翹曲變形等情況,需及時(shí)清理漏脂,并按工藝要求更換新密封圈。
1.4 縮小液壓拉伸器拉伸頭尺寸
與液壓拉伸器供應(yīng)商進(jìn)行技術(shù)溝通,縮小拉伸頭外形尺寸,避免液壓拉伸器現(xiàn)場作業(yè)時(shí)擠壓損壞密封圈;進(jìn)一步規(guī)范現(xiàn)場安裝工藝,增加一項(xiàng)“液壓拉伸器現(xiàn)場作業(yè)時(shí),檢測拉伸頭與密封圈距離”的工序。
2 改善變槳軸承內(nèi)部結(jié)構(gòu)
2.1 溝道底部溝槽
變槳軸承溝道結(jié)構(gòu)設(shè)計(jì)不僅影響潤滑脂在軸承內(nèi)部溝道的流動(dòng)性,也影響與溝道相連接的一段排脂孔的直徑。潤滑脂的流動(dòng)性與其流經(jīng)的截面形狀及面積有關(guān),截面越小,流動(dòng)性越差。
某供應(yīng)商設(shè)計(jì)的變槳軸承溝道內(nèi)部結(jié)構(gòu)如圖7a所示,溝底全部為圓弧過渡,經(jīng)風(fēng)場實(shí)際驗(yàn)證這種溝道截面形狀不利于潤滑脂在溝底的流動(dòng)。改進(jìn)后的溝道截面形狀如圖7b所示,溝底增加了矩形溝槽,從而增加了潤滑脂的流動(dòng)性。試驗(yàn)結(jié)果表明,溝道截面形狀改進(jìn)后潤滑脂可從排脂孔順暢排出,且密封圈無鼓包、漏脂現(xiàn)象。
圖7 某變槳軸承溝道結(jié)構(gòu)
2.2 改善軸承脂孔尺寸與分布結(jié)構(gòu)
GB/T 29717—2013《滾動(dòng)軸承風(fēng)力 發(fā)電機(jī)組偏航、變槳軸承》規(guī)定變槳軸承注脂螺紋孔規(guī)格一般為M10 mm×1 mm,排脂螺紋孔規(guī)格為M14 mm×1.5 mm,當(dāng)有特殊要求時(shí)排脂孔數(shù)量、位置和規(guī)格由軸承制造商與風(fēng)電機(jī)組制造商協(xié)商確定。注脂孔與排脂孔結(jié)構(gòu)如圖8所示。
圖8 注脂孔和排脂孔結(jié)構(gòu)示意圖
由圖8可知,整個(gè)排脂通道為階梯結(jié)構(gòu),分為軸承外側(cè)與集脂瓶相接的螺紋孔部分和靠近軸承內(nèi)側(cè)與溝道相連接的光孔部分。潤滑脂流經(jīng)的截面面積越小,排出時(shí)阻力越大,因此,在軸承結(jié)構(gòu)允許的情況下,適量增加軸承排脂孔外側(cè)連接螺紋孔的直徑和深度,盡量使排脂螺紋孔接近溝道,以減小潤滑脂排出的阻力。排脂孔靠近溝道的光孔部分由于受溝底設(shè)計(jì)槽寬限制,一 般直徑為9 ~12 mm,若改善軸承溝底結(jié)構(gòu),增大槽寬,可考慮增加排脂孔靠近溝道的光孔部分的直徑,有利于排脂。
變槳軸承排脂孔與注脂孔一般均為間隔分布,排脂孔軸向位置處于溝道中心。
3 合理選擇潤滑脂及集中潤滑系統(tǒng)設(shè)置
3.1 選擇合適的潤滑脂
根據(jù)變槳軸承的實(shí)際工況、潤滑脂的稠度及其與密封圈的兼容性等選擇合適的潤滑脂。潤滑脂使用溫度為-40~150℃,應(yīng)具備抗微動(dòng)磨損性、極壓性、抗水性、防腐性和泵送性良好等性能。
3.2 選擇合適的注脂量及潤滑系統(tǒng)控制策略
強(qiáng)制要求變槳軸承最多只能加注70%的填充量,且使用集中潤滑系統(tǒng),不建議采用人工注脂的方式。
考慮到變槳軸承不運(yùn)行或機(jī)組長時(shí)間停機(jī)狀態(tài)時(shí)集中潤滑系統(tǒng)仍按其預(yù)設(shè)好的固定程序繼續(xù)注脂,因此需對(duì)集中潤滑系統(tǒng)的控制策略進(jìn)行優(yōu)化,更改注脂控制方式為變槳軸承運(yùn)行時(shí)注脂(此時(shí)所需注脂壓力遠(yuǎn)小于密封圈的密封壓力),不運(yùn)行時(shí)不注脂。同時(shí)參考變槳軸承變槳的角度、速度、時(shí)間及累計(jì)變槳時(shí)間等因素設(shè)計(jì)控制策略,確定注脂的頻率、時(shí)間等各項(xiàng)指標(biāo)。另外,集中潤滑系統(tǒng)應(yīng)根據(jù)現(xiàn)場的外界溫度進(jìn)行調(diào)整,低溫時(shí)潤滑脂的稠度大,泵送性較差,此時(shí)需要提高注脂頻率;高溫時(shí)潤滑脂的稠度小,泵送性較好,此時(shí)需要降低注脂頻率。
針對(duì)集中潤滑系統(tǒng)的壓力泵或輸脂管中的空氣未完全排空造成漏脂的問題,可以在集中潤滑系統(tǒng)安裝完成后,與變槳系統(tǒng)進(jìn)行聯(lián)合調(diào)試,通過實(shí)際運(yùn)行集中潤滑系統(tǒng)檢驗(yàn)變槳軸承溝道中是否有殘存空氣并進(jìn)行充分排除。
3.3 增加廢脂清除系統(tǒng)
如圖9所示,廢脂清除系統(tǒng)的工作原理為:啟動(dòng)液壓泵,壓力油通過動(dòng)力管A驅(qū)動(dòng)廢油吸排脂器將軸承內(nèi)的廢油吸入吸排脂器內(nèi)腔,然后分控箱啟動(dòng)二位四通閥,系統(tǒng)換向,壓力油通過動(dòng)力管B驅(qū)動(dòng)廢油吸排脂器將排脂內(nèi)腔中收集到的廢脂通過集廢油管集中收集到集油箱。
另外可采用真空袋代替集脂瓶來收集廢脂,或者縮短廢脂排出管路,增大集脂瓶管口直徑等方法來改善廢脂不易排出的情況。
1一動(dòng)力管B;2—集油箱;3—液壓泵;4—廢油吸排脂器;5—分控箱;6—?jiǎng)恿蹵;7—集廢油管
圖9 廢潤滑脂清除系統(tǒng)結(jié)構(gòu)原理圖
(第一部分請(qǐng)見網(wǎng)站;風(fēng)電機(jī)組變槳軸承漏脂分析及改進(jìn)措施(1))
(來源:軸承雜志社)
軸研所公眾號(hào) 軸承雜志社公眾號(hào)
營銷熱線
0379-64367521
0379-64880626
13693806700
0379-64880057
0379-64881181